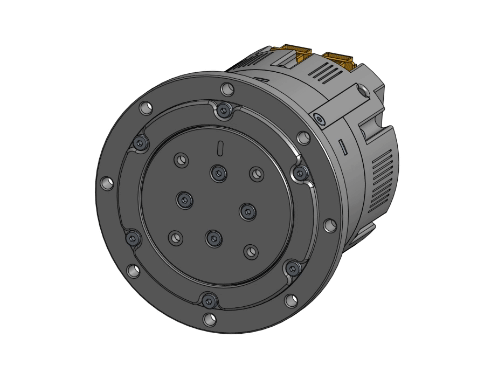
Project Goal:
My goal was to design and manufacture a high-gear ratio, split ring, all-in-one harmonic drive BLDC actuator. I wanted to utilize the high resolution production capability of FDM 3D-printing to produce the fine details on both the flexspline and split circular splines of the drive, as well as the custom wave generator geometry and outer housing. Instead of relying on the typical thin-walled bearing, my design leverages embedded cylindrical rollers along the surface of the wave generator. This allows low friction contact between the flexspline and the wave generator.
Prototyping and Design:
Before designing the actuator, I developed a double-circular-arc common tangent tooth profile CAD drawing to automatically generate the flexspline and split circular splines models for 3D-printing. The model takes in the number of teeth, the pitch line diameter, and other necessary tooth meshing parameters and generates the resulting flexspline or circular spline. Figure 1 displays the base parameter-driven tooth sketch.
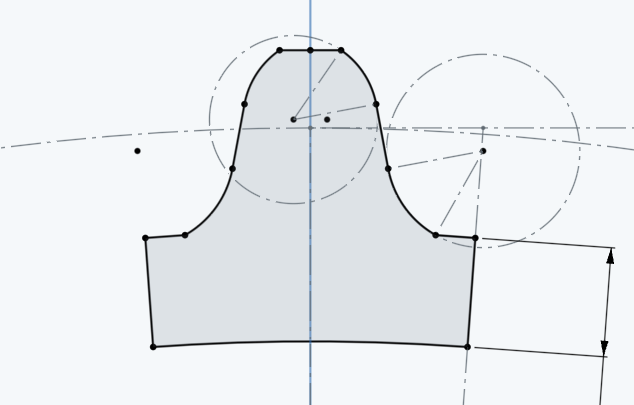
Figure 1: Circular Tangent Tooth Profile Example
In a typical industrial harmonic drive, the flexspline is made of a stainless steel deep-drawn cup whose gear teeth are skived or hobbed into the lip. As the wave generator deforms the lip of the cup, the cup’s teeth mesh with a fixed outer circular gear. This induces a rotation of the cup, which in turn drives the output of the gearbox.
When I translated this design to FDM 3D printing, where printed parts are weak against loads applied parallel to the layer lines, I found that the standard flexspline cup design continued to shear under even a minor load. To overcome this, I opted for a split ring design where the flexspline is a continuous printed extrusion (see Figure 2).
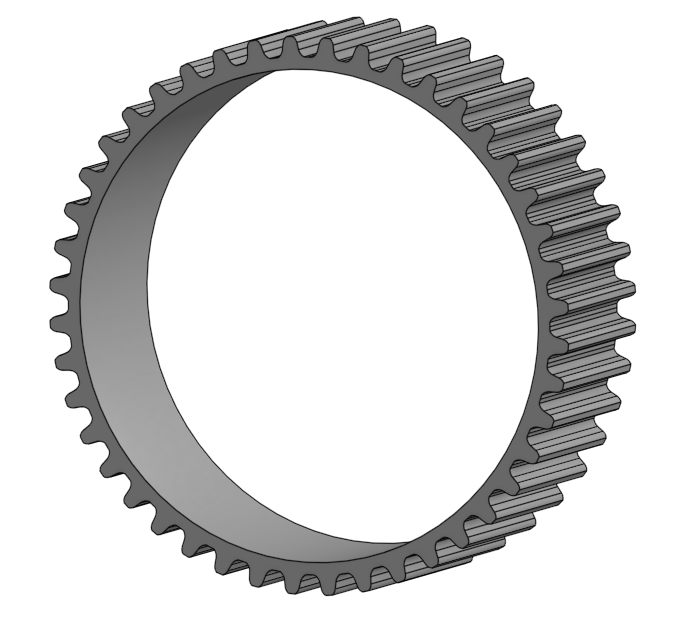
Figure 2: Generated Flexspline
The split ring harmonic drive actuator utilizes two circular splines (one fixed and one rotating) to accomplish the desired high-gear reduction. A fixed circular spline with the same number of teeth as the flexspline balances the load on the flexspline, while the rotating circular spline performs the gear reduction and drives the output.
Figure 3 below displays a section view of the completed actuator and shows the fixed and rotating circular splines.
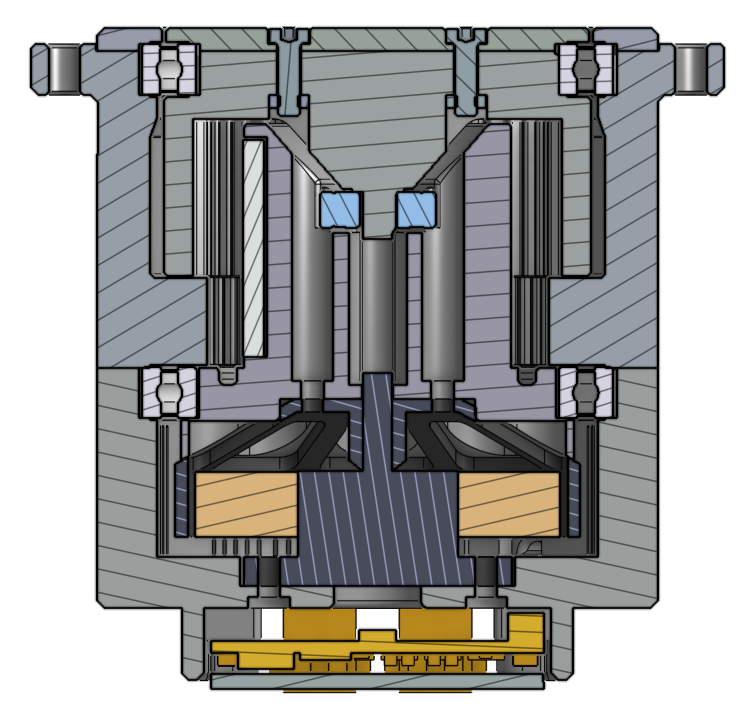
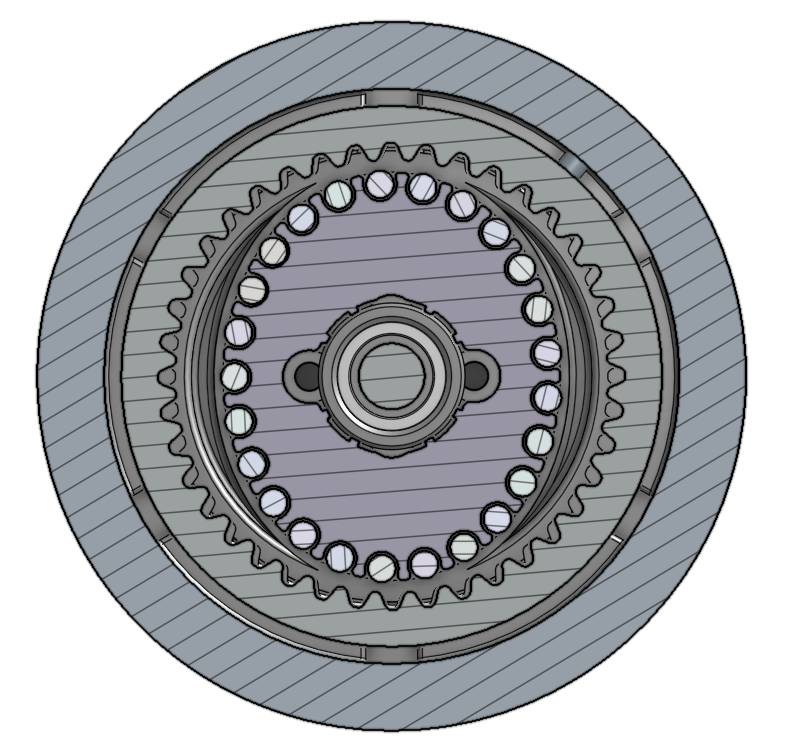
Figure 3: Section View of Completed Harmonic Drive Actuator
Video 1 demonstrates how I connected the custom wave generator to the BLDC motor. I rigidly affixed the wave generator to the front face of the BLDC motor using four M3 bolts.
Video 1: Mounting Wave Generator
In typical harmonic drives, a thin-walled bearing is press-fit onto the elliptical wave generator transferring the rotation to the flexspline. These thin-walled bearings are typically custom designed and thus expensive and out of spec for a low-cost actuator build. Instead, I designed a custom wave generator with integrated cylindrical rollers, which could transfer rotation to the flexspline without a thin-walled bearing. I placed the cylindrical rollers into pockets on the edge of the wave generator. Once I installed the flexspline, the rollers were constrained in their positions. Video 2 demonstrates how I assembled the custom wave generator.
Video 2: Mounting the Flexspline
After I mounted the wave generator and flexspline, I mounted the assembly onto the bottom housing. The bottom support bearing aligns the wave generator into the bottom actuator housing. I affixed the bottom mount of the BLDC drive motor using eight M3 bolts.
Video 3: Mounting the Bottom Housing
The Moteus motor driver, a BLDC closed loop integrated controller, drives the actuator. A magnetic encoder underneath the driver board measures the current angle of the BLDC motor. I mounted the Moteus driver using four M2.5 bolts and protected it with a cover.
Video 4: Mounting the Motor Driver
Video 5 demonstrates how I connected the fixed circular gear to the bottom actuator housing.
Video 5: Mounting the Upper and Lower Housing
Lastly, I installed the rotating circular spline gear. The rotating gear has two more teeth than the flexspline, thus facilitating the gearbox reduction. It is supported by both a small bearing in the wave generator and a large bearing in the outer housing.
Video 6: Mounting the Output Gear
Final Product:
Video 7: Final Assembled Actuator
Video 7 shows the fully assembled harmonic drive gearbox. The next step now is to put this actuator to work!