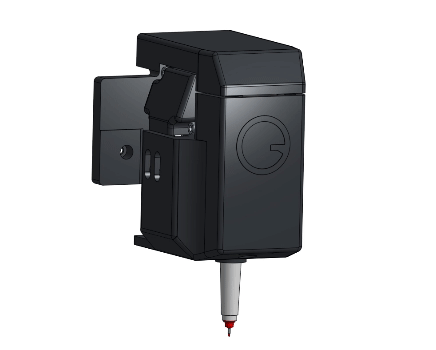
Project Goal:
The goal of this project was to create a novel-geometry automatic tool changing end effector specifically for picking up thin-tip Sharpies. Ultimately, this end effector is intended to automate a pen plotter machine. It would allow multiple pens to be placed in a tool carriage and would facilitate color changes through GCODE.
Requirements:
My design needed to leverage a 3D-printed central flexure that I designed to clamp onto cylindrical tools (e.g. Sharpies). Figure 1 shows a rendering of the flexure. The flexure has a cylindrical cut through the center that allows the top and bottom to align the tool. The center section is relieved such that two elastic bands can apply preload to the tool, clamping down on the surface when the flexure is uncompressed. When compressed vertically, the mirrored lever arms of the flexure force the center section outward, expanding the clamp and releasing the tool.
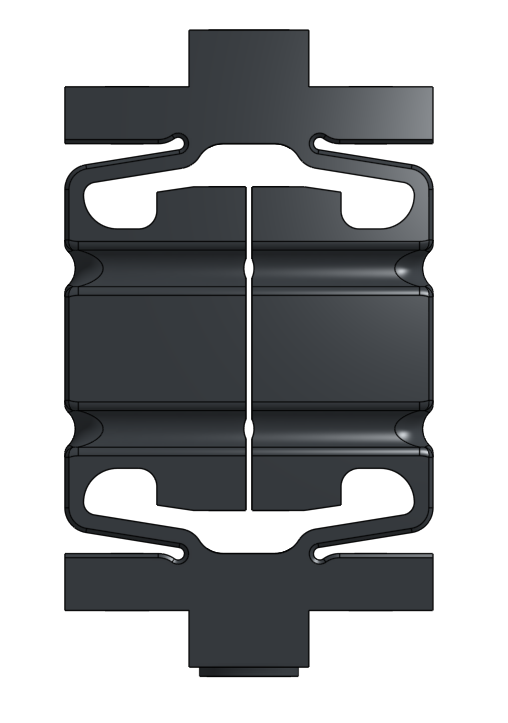
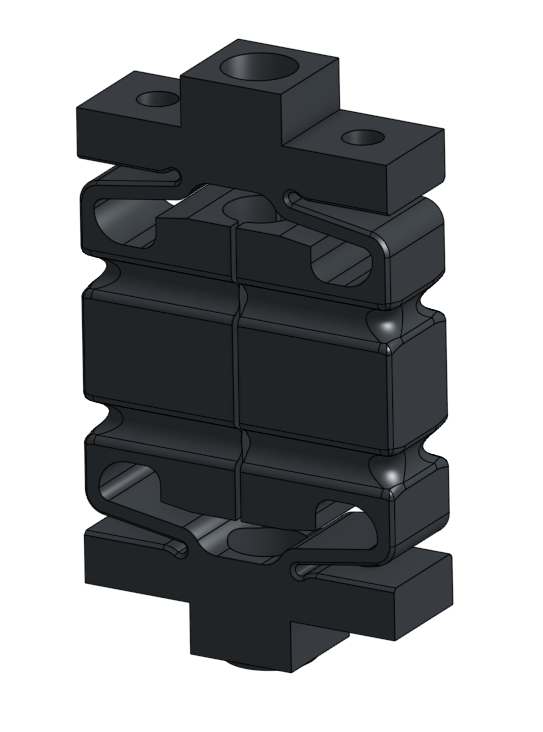
Figure 1: Clamping Flexure Rendering
Prototyping and Design:
To keep the overall design compact, I decided to use two integrated lead screw micro gear motors to drive the vertical compression of the actuator. Figure 2 depicts a section view of how the dual motors mount into the top portion of the actuator and interface with the retained M4 nut that constrains the motion of the lower portion.
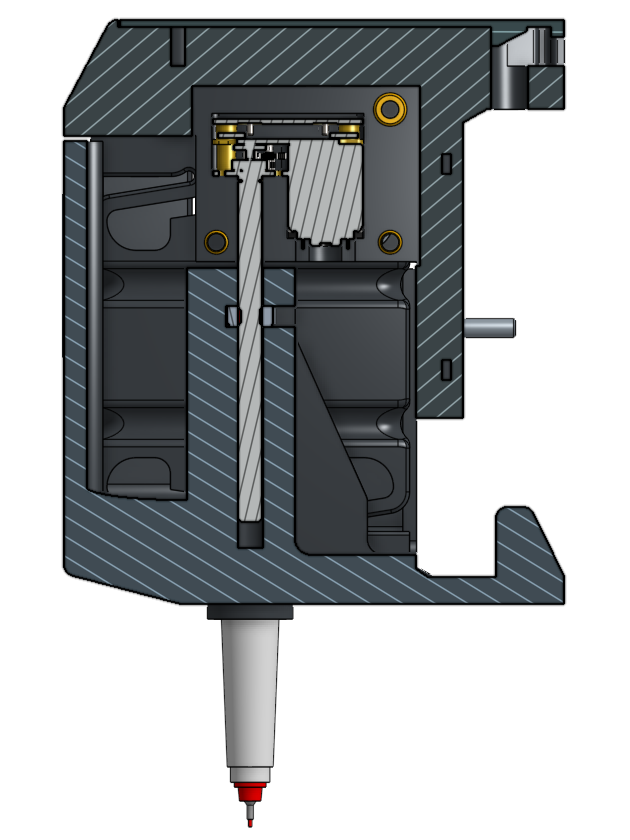
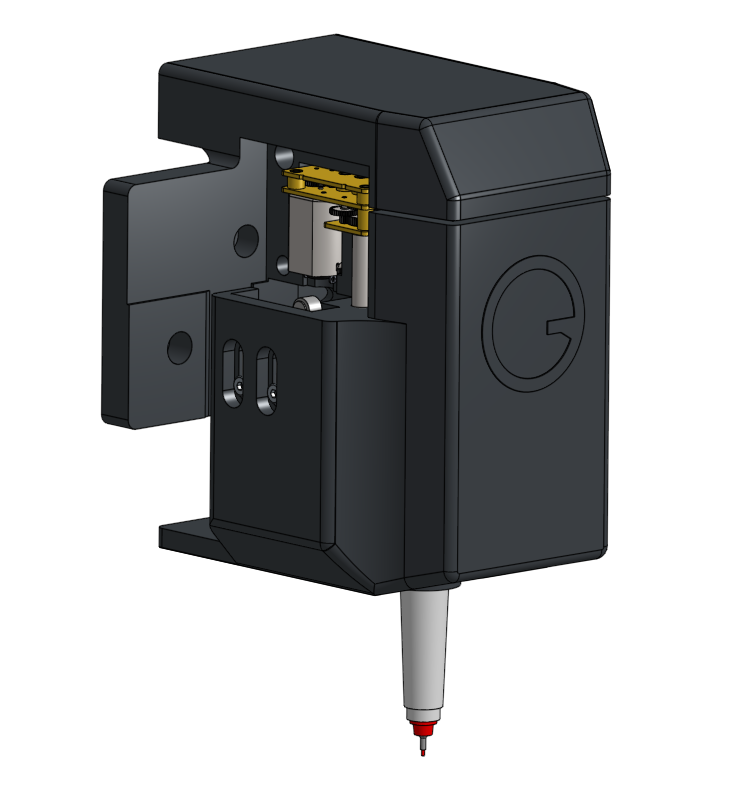
Figure 2: Completed Actuator Rendering
A 10 kg load cell was mounted such that its cantilevered end sits directly in line with the end of the tool. During the tool changing process, the end effector is lowered until the tool makes contact with the load cell, signaling success. Once the pen is in contact with the load cell, any axial force applied to the pen will be transferred to the load cell, so the load cell can be used for force feedback when writing.
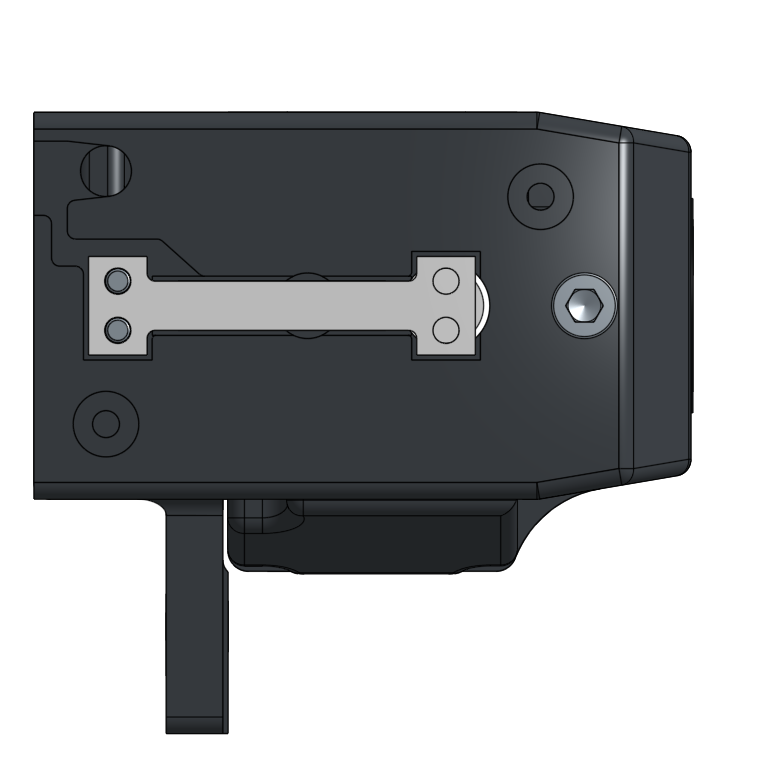
Figure 3: Loadcell Mounting in Actuator
Final Design:
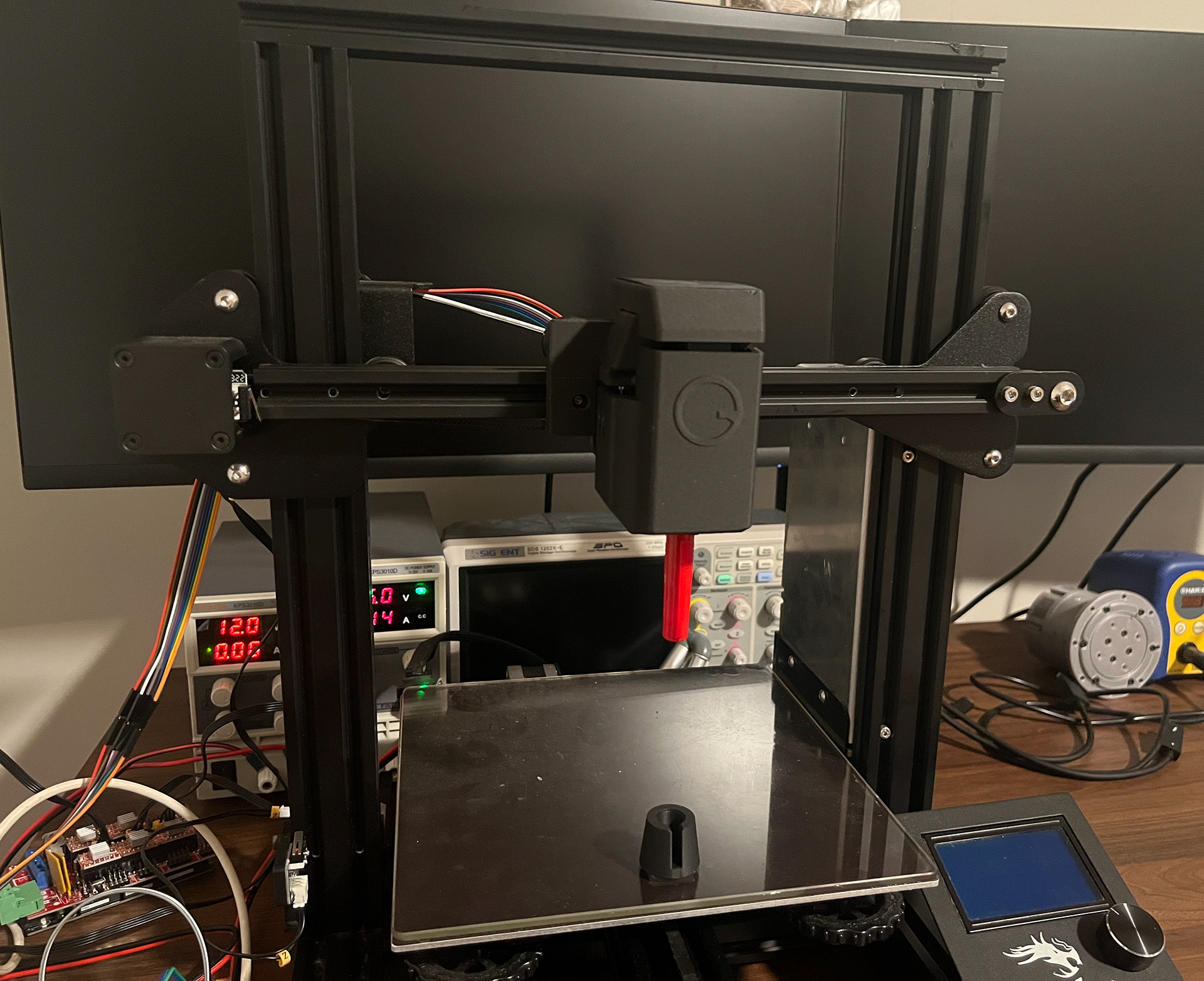
Figure 4: Completed Tool Changer mounted on Ender 3
I fabricated and mounted the completed actuator onto a modified Ender 3 printer, which serves as the base platform for the pen plotter.
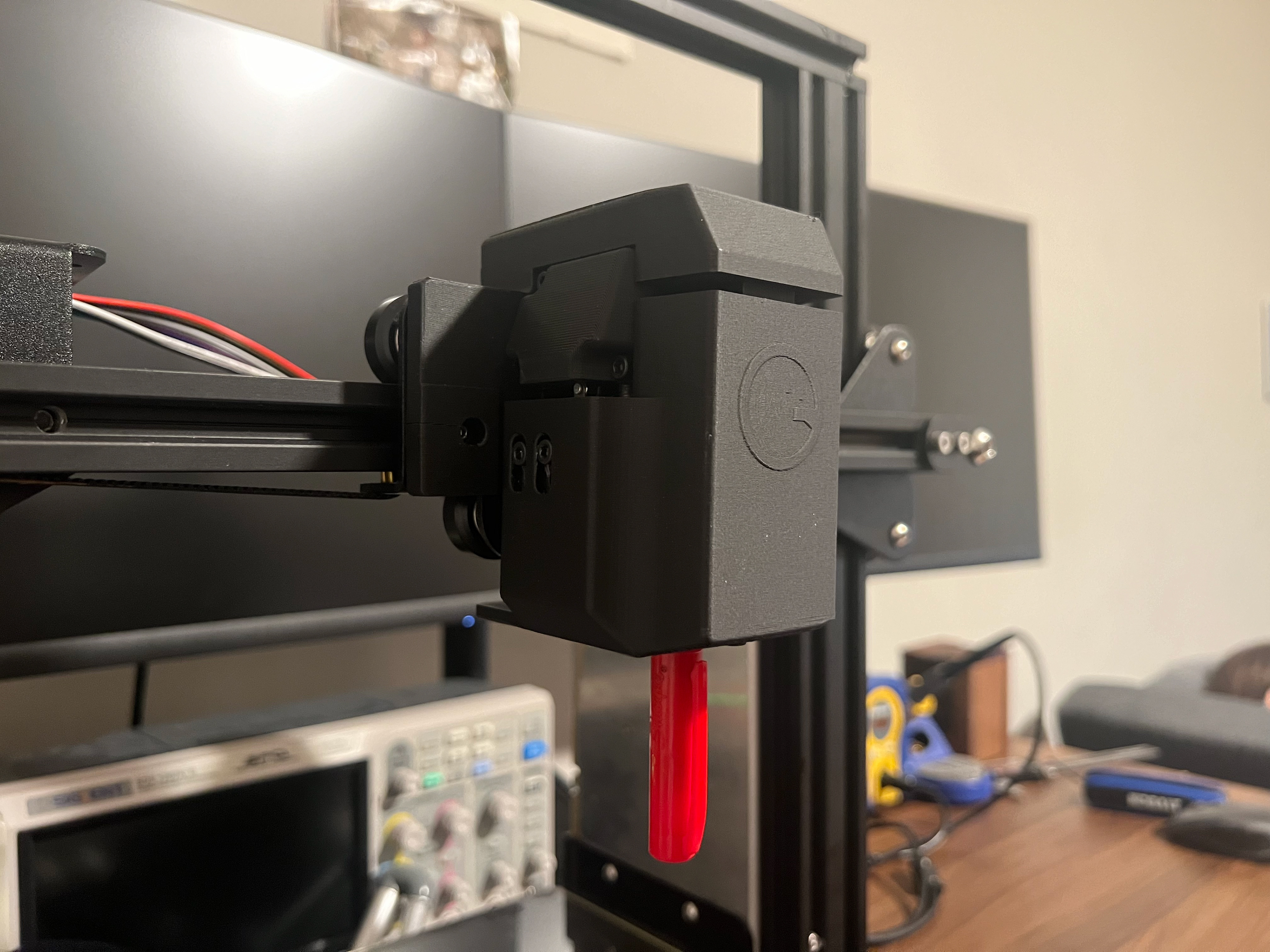
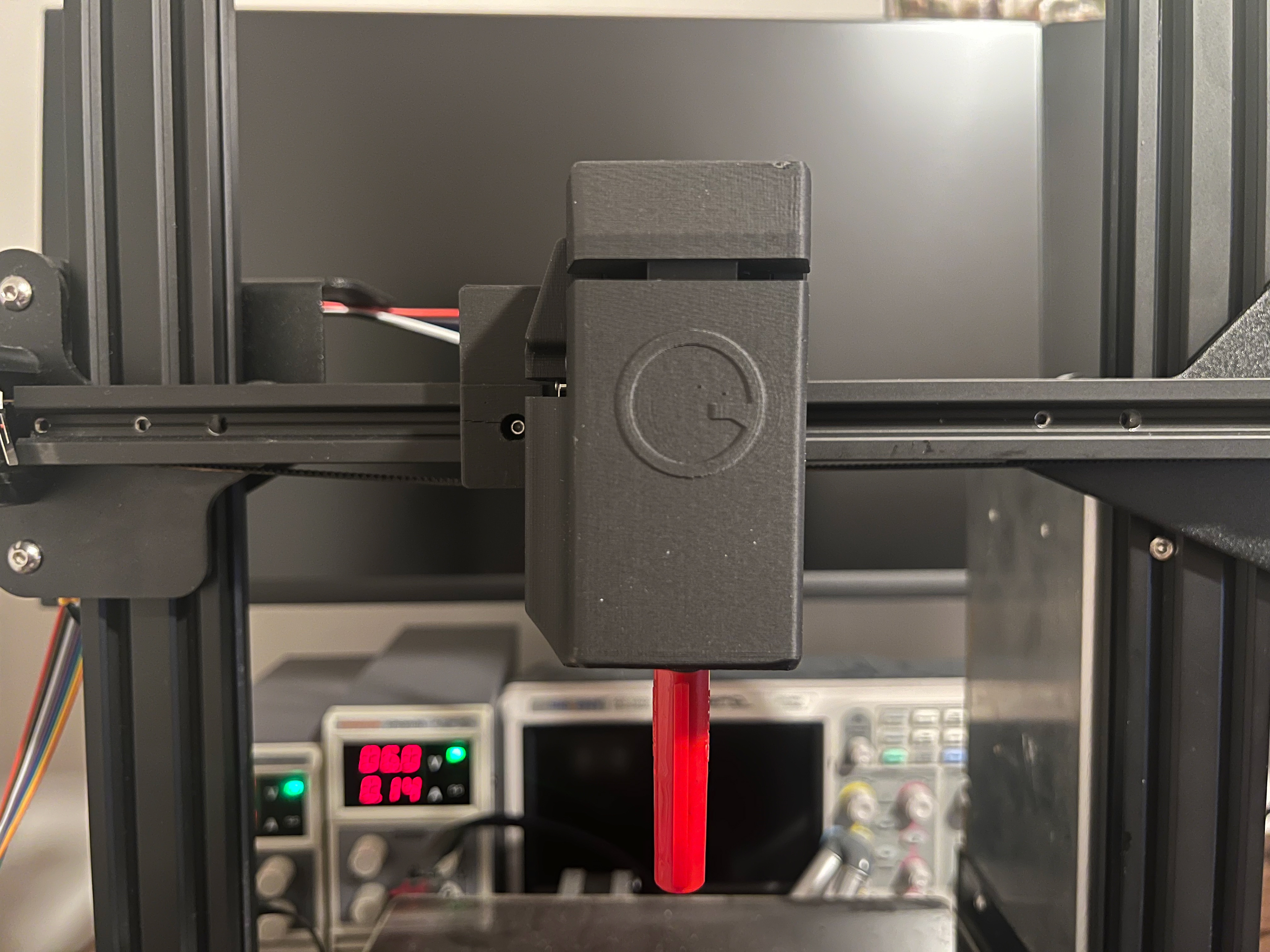
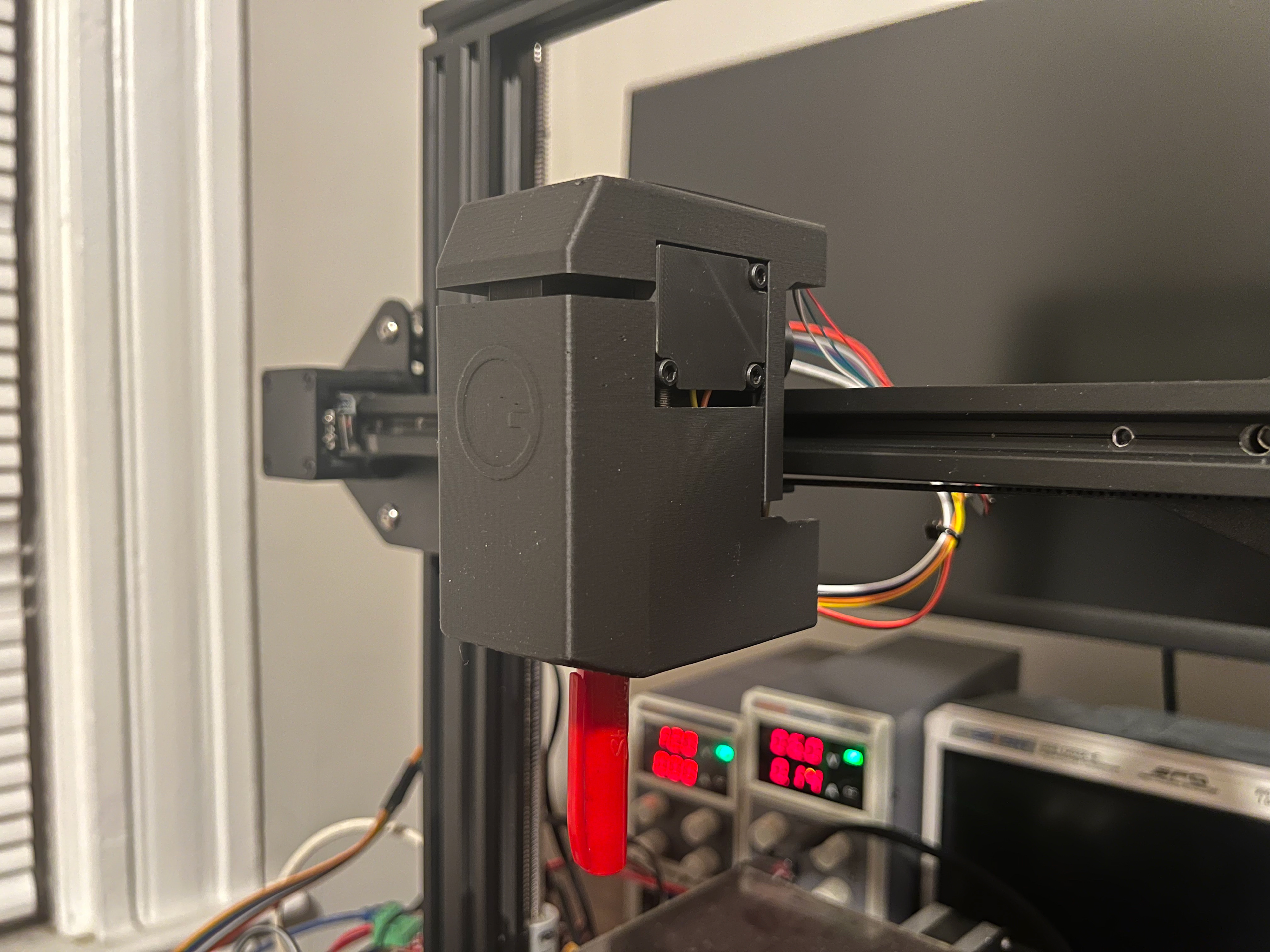
Figure 5: Close-up Views of the Mounted Tool Changer
I replaced the proprietary control board with a Ramps 1.4 board running Marlin. I wrote custom GCODE scripts and injected them into the control board through Pronterface to control the pick operation and open-close actuations. The videos below demonstrate the actuator's smart tool detection and tool changing abilities.
Video 1: Demonstration of Active Tool Detection
Video 2: Auto Tool Pickup Demonstration