
Project Goal:
My design group was tasked by the PoWeR (Physiology of Wearable Robotics) lab at the Georgia Institute of Technology to redesign their ankle-exoskeleton actuator by removing the previous planetary gear set, and replacing it with a custom simulation-validated planar torsional spring.
Requirements:
The motion of the ankle produces a linear force, so the custom planar torsional spring must have a linear spring constant or be approximately linear within the range of motion of the ankle. The planar torsional spring must compress and extend without self collision or out of plane movements throughout the full operating range. The spring must be appropriately sized to avoid colliding with the ground or impeding other aspects of the exoskeleton.
The torsional spring must fit within these engineering specifications:
Linear spring constant: 1.5 Nm/deg
Maximum torsional load: 80 Nm
Maximum outer diameter of torsional spring: 100 mm
Maximum torsional load: 80 Nm
Maximum outer diameter of torsional spring: 100 mm
The PoWeR lab plans to test our design in a 15 week long, multiple participant study where exoskeleton users will hop at their desired pace for 5 minutes, 3-4 times a week. To support the repeated use of the spring under different participant conditions, the spring must be designed to have infinite life.
Prototypes:
After an in-depth literature review, we began by referencing a patented linear torsional spring design. In this design, the spring geometry only had two connection points between the inner and outer fixture points. We scaled it up to our maximum outer diameter dimensions and simulated the design under our loading conditions. We found that the design would self collide during loading. To increase the torsional stiffness, we incremented the number of inner and outer fixture points, but found that while this fixed the self collision, the further constrained spring yielded under the operating stress due to its thin geometry.
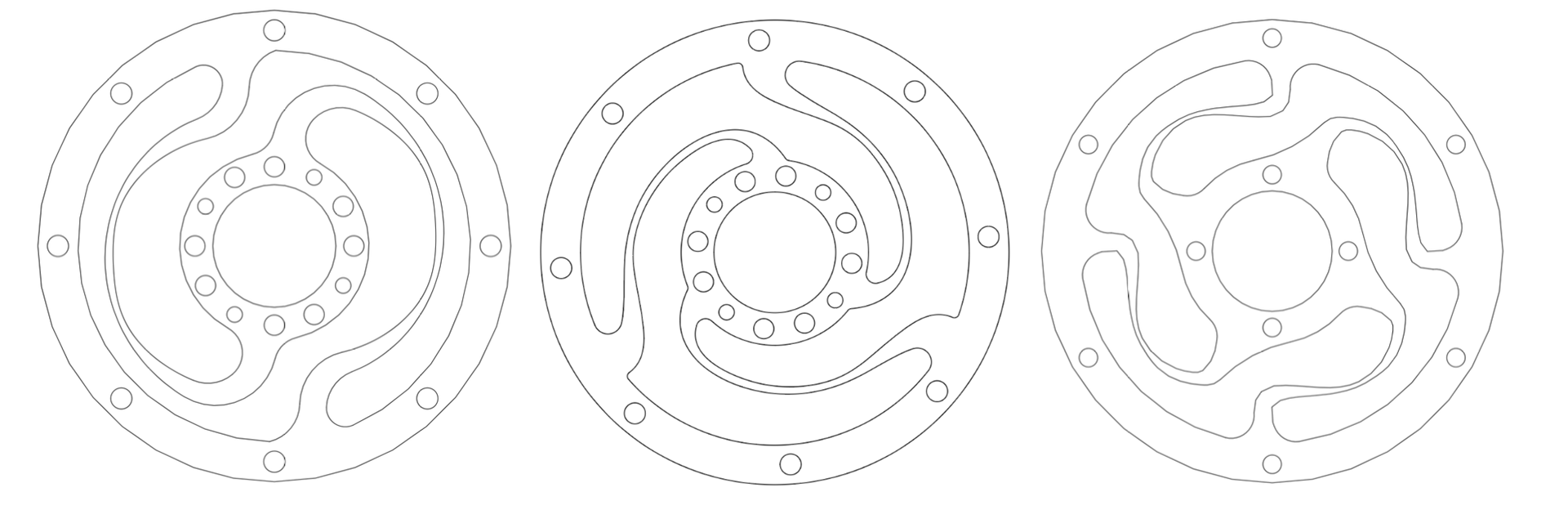
Figure 1: Prototype Torsional Springs
Moving away from the thin geometry, we simplified the spring members to have a uniform thickness. The designs in Figure 2 are inspired by a beam in bending. Although we found that the spiral nature led to uniform stress concentrations across the spring, we also noticed self collisions when attempting to reach the operating range of motion. Once we altered the spline thickness and gap, we were able to prevent the self collisions. In our final proposed design, we also smoothed the contact points between the inner and outer races, which minimized stress concentrations.
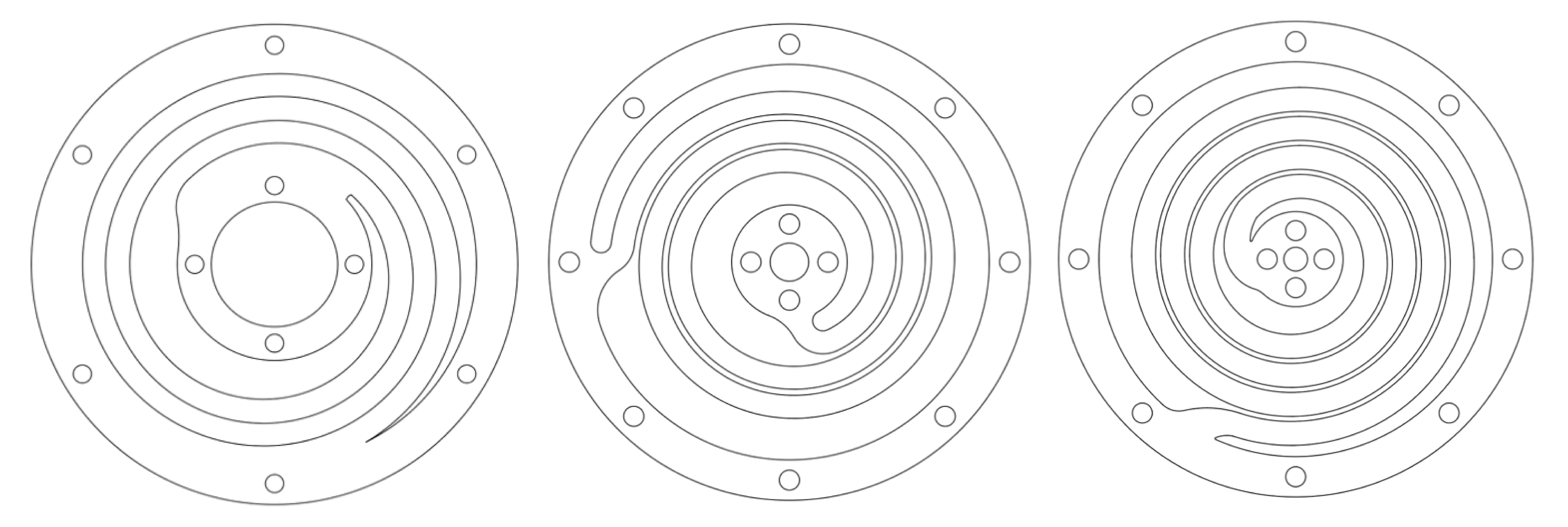
Figure 2: Final Torsional Spring Iterations
Final Product:
Figure 3 shows the final design of the planar torsional spring. To meet the engineering requirements, the design would have to be made out of titanium with a 2" thickness. While 2" thick material is cost prohibitive, we proposed a flat stock application that would allow the stacking of thinner springs to reach the desired thickness. This way, the spring could be manufactured with fiber laser cutting, water jet, or wire EDM cutting. We compiled our final results, calculations, and manufacturing recommendations into a client report for the PoWeR lab.
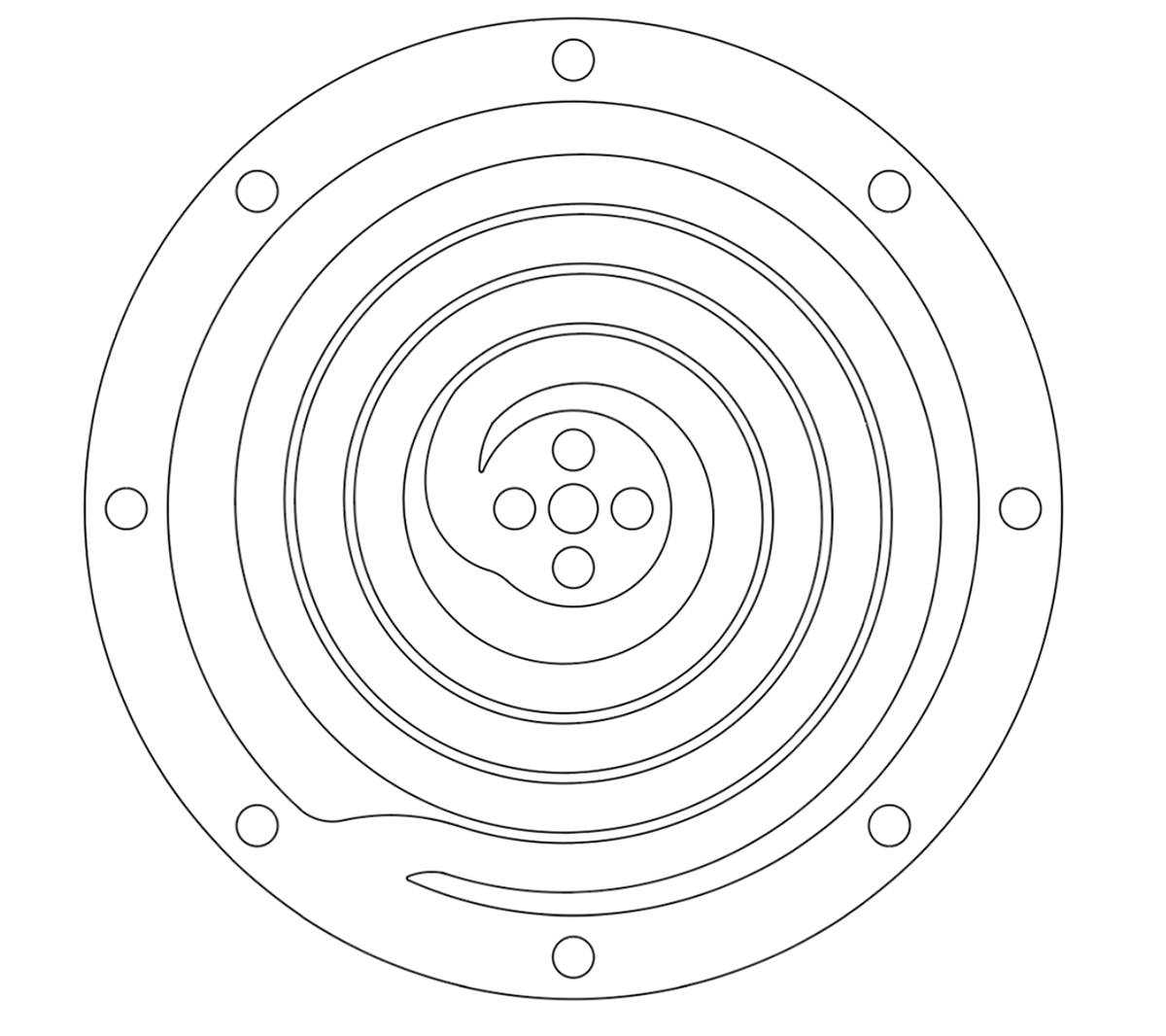
Figure 3: Final Torsional Spring Design